Cutting-Edge Robotic RFID Tagging and Colour Coding
The team at Industry-Connect coupled their industry leading automation know-how, with design and manufacturing expertise to deliver a flawless execution, the blueprint for future InfraBuild projects
Background
InfraBuild, one of Australia’s leading steel manufacturers, is known for its commitment to quality and innovation.
At its Sydney Rolling Mill, InfraBuild plays a critical role in producing high-grade steel for major construction and infrastructure projects nationwide. The facility is recognized for its cutting-edge approach to steel production, continuously driving operational efficiency and sustainability. With a focus on maintaining its leadership in the industry, InfraBuild consistently explores advanced technologies to enhance productivity and ensure the highest standards of quality.
In recent years, InfraBuild has taken bold steps to drive product sustainability and traceability. By leveraging state-of-the-art technologies, the company has established benchmark infrastructures, enabling full visibility into the lifecycle of its products. This initiative not only enhances operational transparency but also sets a new standard in the market, positioning InfraBuild as a leader in sustainable and responsible steel manufacturing.
Challenge
As a major supplier to Australia’s construction and infrastructure sectors, InfraBuild faces the critical challenge of maintaining a highly reliable and sustainable supply chain. The steel products produced at its Sydney Rolling Mill, including the premium “Sense 600” range, are essential components in large-scale, safety-critical projects like bridges, high-rise buildings, and transportation infrastructure.
For these applications, quality and consistency are nonnegotiable, making traceability and supply chain reliability key to meeting stringent regulatory and performance standards.
In addition, operating a production facility in Australia presents unique pressures. Increasing overhead costs, including energy and labour, make it imperative for InfraBuild to continually seek ways to optimize efficiency while remaining competitive with international producers. The demand for sustainability adds another layer of complexity, requiring not only the production of high-quality steel but also the assurance that each product’s environmental impact is minimized across its lifecycle.
Meeting these challenges requires innovation in every aspect of operations, from minimizing waste to ensuring that products are properly identified and traceable throughout their journey— from production to final use. Achieving this level of precision while managing increasing costs and ensuring sustainable practices is a significant challenge for InfraBuild as they strive to uphold their leadership in the market.
Solution
To tackle the challenges of supply chain reliability, product traceability, and increasing production costs, InfraBuild partnered with Industry-Connect and its leading technology partners, Green Project and S+P Samson. Known for their innovation leadership, Industry-Connect and its partners offered InfraBuild a custom-tailored solution, providing close support from the initial stages of development through to implementation, ensuring the solution precisely met their needs.
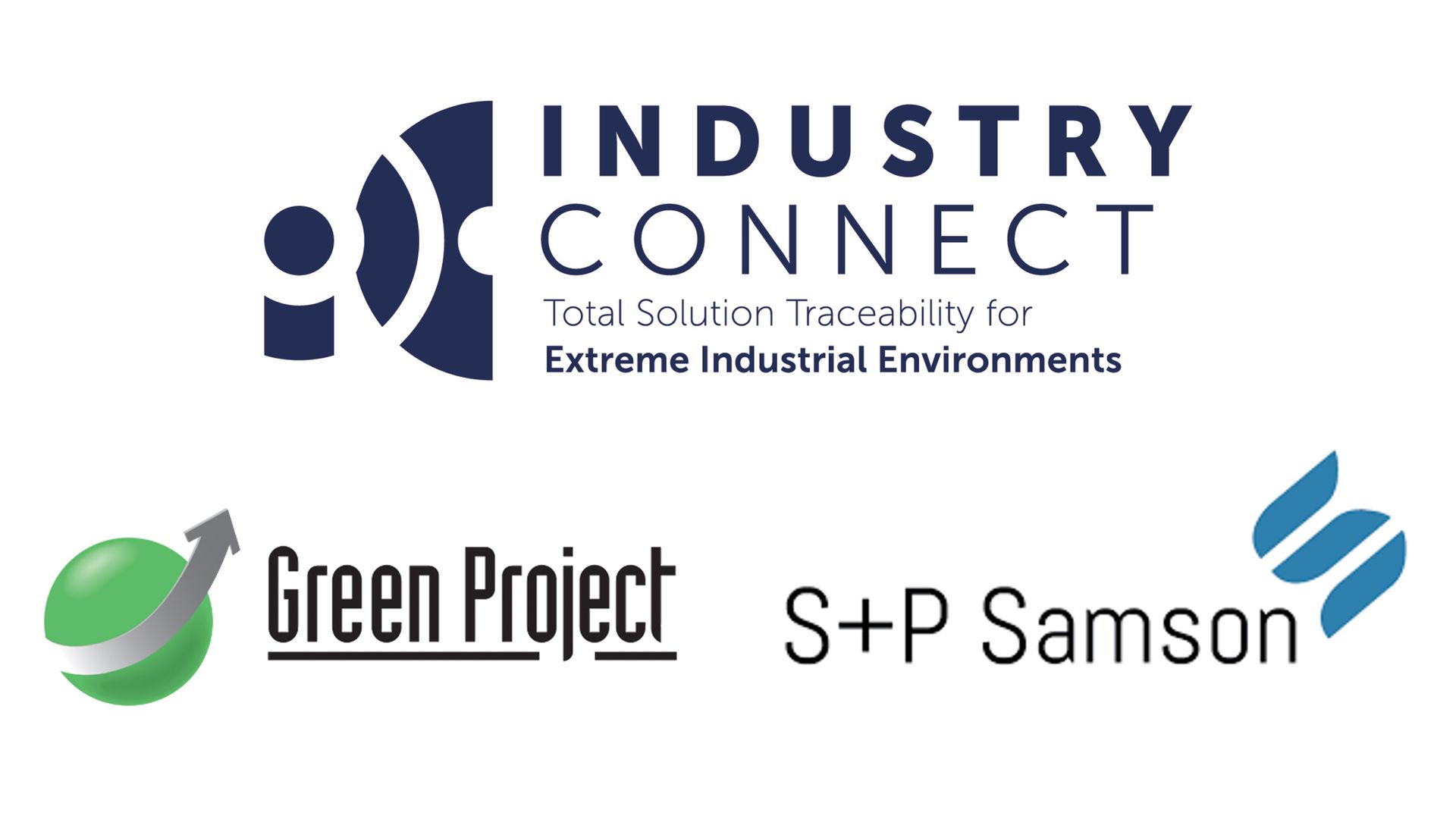
The automated system features a 25-meter long gantry with a carriage housing a six-axis robot, two RFID-enabled printers, and three paint tanks for different coloured paints. This setup allows InfraBuild to automatically tag and colourcode a variety of products, including rounds, flats, angles, and Y-bars, with bundle lengths ranging from 6 to 18 meters.
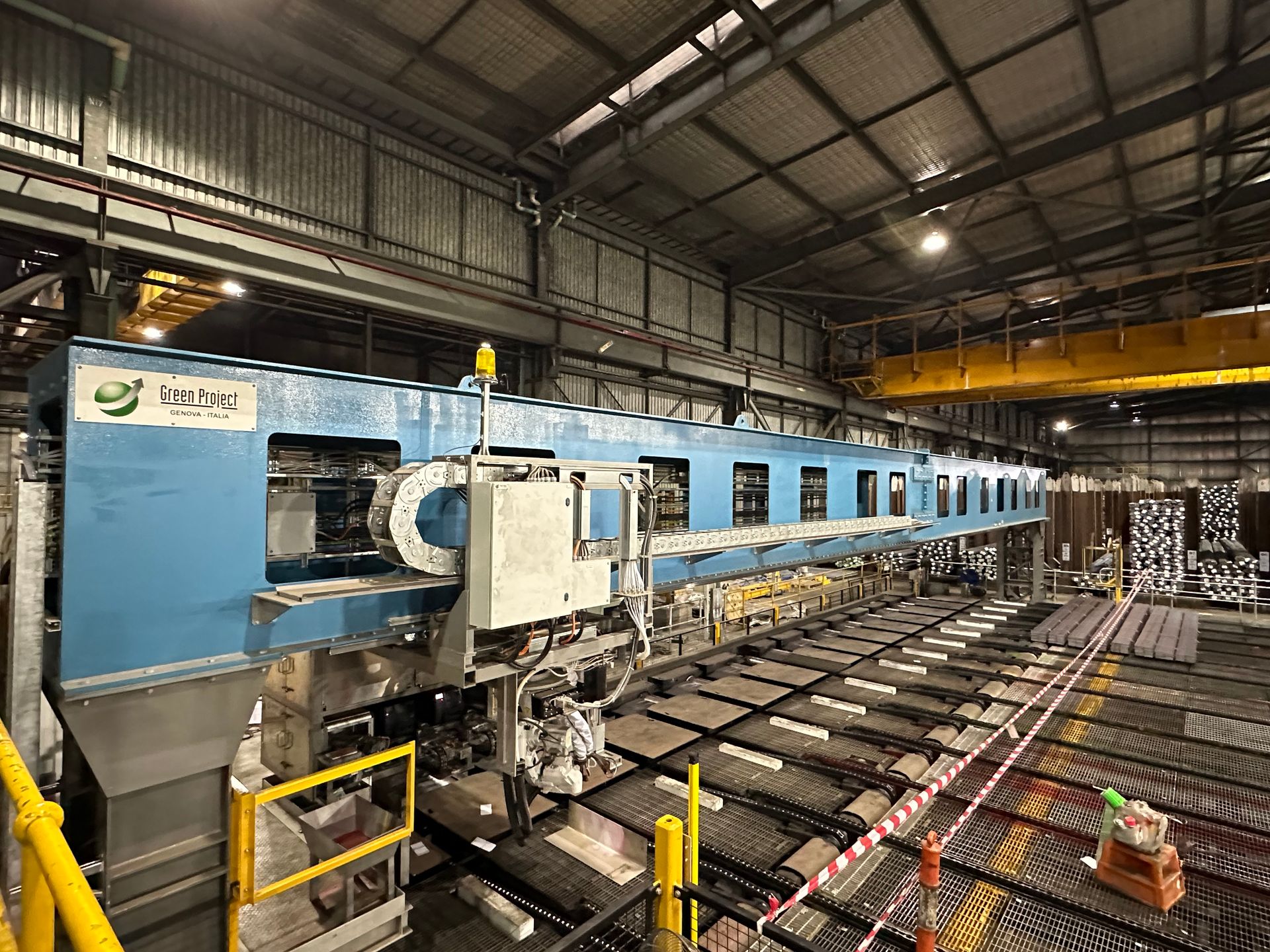
The system includes an automated welding stud dispenser, ensuring precise tag application even in challenging mill conditions. Integrated 3D laser scanners and camera vision systems further enhance operational accuracy by ensuring the quality of bundle packing, correct tag printing and readability, identifying the optimal tagging location for each bundle, and verifying successful process completion.
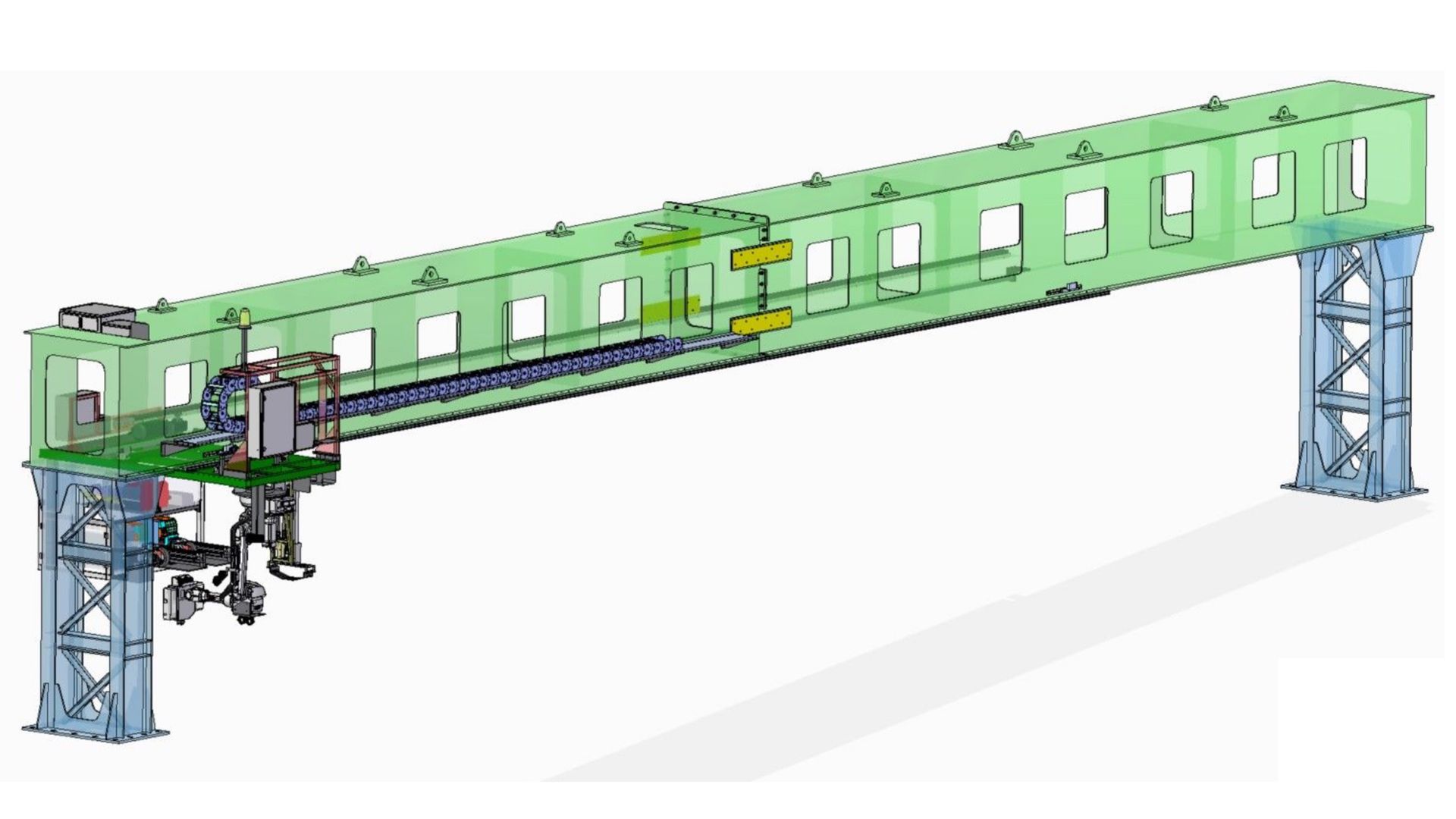
In addition, the system is directly integrated with the plant’s Level 2 control system, enabling automated, bidirectional data transfer for real-time exchange of bundle and marking data. This seamless integration ensures that InfraBuild’s tagging and tracking process is fully synchronized with production operations, increasing both efficiency and reliability.
“The system installed in InfraBuild demonstrates a fully customized innovative ‘all in one’ solution, integrates several state-of-the-art technologies such as 3D laser scanning, smart vision for codes identification, RFID printing and tagging, all combined on a single robotized carriage,” says Andrea Bruno, Project Manager at Green Project. S+P Samson’s RFID-enabled tags offer significant advantages in product traceability.
These highly durable tags are resistant to high temperatures, allowing InfraBuild to mark products while they are still hot, ensuring full product identification and traceability prior to any manual handling process.
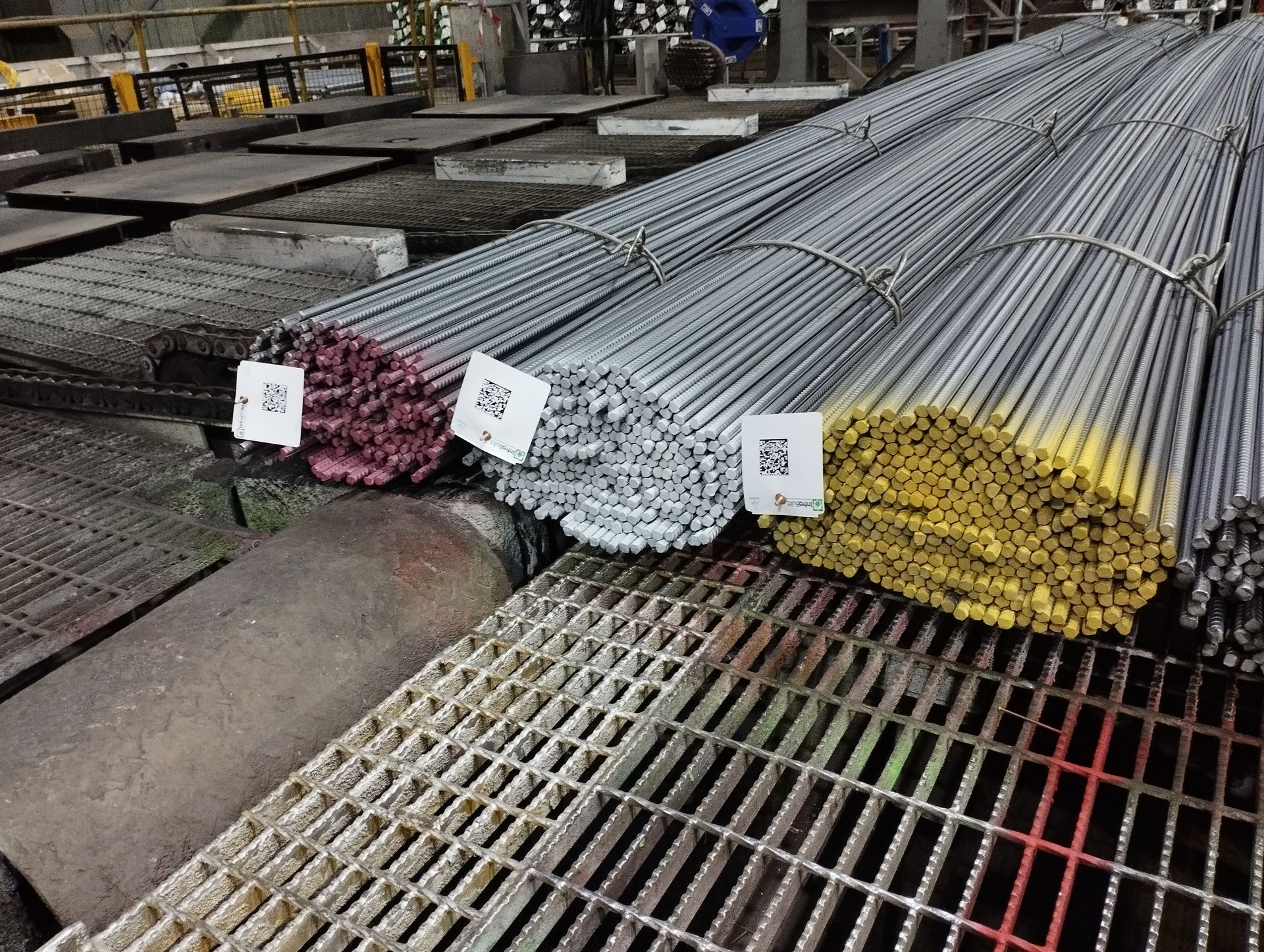
This capability enhances operational safety, as well as providing real-time traceability for monitoring the location and status of steel bundles throughout the supply chain.
The technology ensures transparency, sustainability, and compliance with regulatory standards, while also improving traceability for critical infrastructure projects, including high-grade products like “Sense 600” steel.
A key advantage of this solution is the elimination of manual processes and the associated risk of human error. By automating tagging and tracking operations, InfraBuild significantly reduces labour costs and the potential for mistakes in product identification and data entry.
This streamlined workflow directly translates into:
- Lower Overhead,
- Increased Operational Efficiency,
- More Reliable Production Output,
Making the Sydney Rolling Mill more competitive in a market facing rising production costs.
With the expertise and innovation brought together by Industry-Connect, InfraBuild is now positioned to benefit from both operational and overhead improvements, setting a new standard for sustainable and automated steel production.
This partnership and close collaboration with InfraBuild provided us with the opportunity to develop new and innovative solutions, for example the use of smart vision on a robot to read the code printed on the tag but also to ensure perfect alignment between the stud holder and the welding stud itself during picking phase. Instances like this ensured the delivery of a highly reliable advanced tagging system.
Results
The implementation of the automated tagging and paint marking system, combined with RFID-enabled tags, has delivered significant improvements for InfraBuild at the Sydney Rolling Mill.
Key results include:
- Error Rate Reduction: Achieved 100% performance during Factory Acceptance Test, drastically reducing manual errors and ensuring accurate product identification.
- Automated Tracking: RFID-enabled tags now provide real-time tracking throughout downstream logistics, enhancing transparency and compliance with regulatory standards.
- Cost Savings: Annual savings in the six-figure AUD range, driven by improved efficiency, reduced labor, and overhead cost reductions.
- Fast Payback: The project’s payback time is expected to be 2-3 years, with an impressive ROI of 30-50%.
- Long-Term Impact: The system optimizes resource utilization, boosts competitiveness, and sets a new benchmark for automated and sustainable steel production.
InfraBuild celebrates the successful commissioning of transformational infrastructure designed to fully automate printing, tagging and painting of bundled reinforcing products at our Sydney mill. Working with our industry partner, Industry-Connect, a highly advanced solution was designed, manufactured and commissioned providing step changes to our traceability, safety, productivity and efficiency. The team at Industry-Connect coupled their industry leading automation know-how, with design and manufacturing expertise to deliver a flawless execution, the blueprint for future InfraBuild projects.
Sharmy Francis, Manager Innovation, InfraBuild